The 9-Second Trick For Alcast Company
Wiki Article
The Ultimate Guide To Alcast Company
Table of ContentsFascination About Alcast CompanyFascination About Alcast CompanySome Known Incorrect Statements About Alcast Company 6 Easy Facts About Alcast Company ExplainedSome Ideas on Alcast Company You Need To KnowThe Buzz on Alcast Company
The subtle distinction depends on the chemical content. Chemical Contrast of Cast Light weight aluminum Alloys Silicon advertises castability by lowering the alloy's melting temperature level and enhancing fluidness during casting. It plays a vital role in permitting intricate mold and mildews to be filled accurately. Additionally, silicon adds to the alloy's strength and use resistance, making it valuable in applications where durability is critical, such as vehicle components and engine parts.It additionally improves the machinability of the alloy, making it simpler to process into completed products. By doing this, iron contributes to the general workability of light weight aluminum alloys. Copper raises electrical conductivity, making it useful in electrical applications. It also improves corrosion resistance and includes to the alloy's overall stamina.
Manganese adds to the toughness of light weight aluminum alloys and improves workability (Foundry). It is typically made use of in wrought aluminum products like sheets, extrusions, and accounts. The visibility of manganese help in the alloy's formability and resistance to fracturing during construction processes. Magnesium is a lightweight element that provides strength and influence resistance to light weight aluminum alloys.
The Single Strategy To Use For Alcast Company
It enables the production of lightweight elements with superb mechanical residential properties. Zinc improves the castability of aluminum alloys and helps manage the solidification process throughout spreading. It boosts the alloy's toughness and firmness. It is typically found in applications where elaborate shapes and great information are essential, such as attractive spreadings and particular automotive components.
The main thermal conductivity, tensile stamina, yield strength, and elongation vary. Amongst the above alloys, A356 has the highest thermal conductivity, and A380 and ADC12 have the cheapest.
Get This Report about Alcast Company
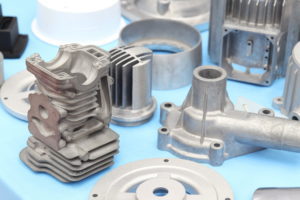
Its unique properties make A360 a useful choice for accuracy spreading in these markets, boosting product sturdiness and high quality. Aluminum Castings. Aluminum alloy 380, or A380, is a commonly made use of casting alloy with several unique qualities.
In precision spreading, light weight aluminum 413 shines in the Consumer Electronic Devices and Power Tools markets. It's generally utilized to craft elaborate parts like smart device real estates, camera bodies, and power device cases. Its accuracy is impressive, with tight resistances as much as 0.01 mm, making certain remarkable item setting up. This alloy's premium corrosion resistance makes it a superb selection for outdoor applications, ensuring check my source long-lasting, sturdy items in the pointed out sectors.
The Definitive Guide for Alcast Company
Once you have made a decision that the light weight aluminum die casting procedure is suitable for your job, an essential following action is selecting one of the most appropriate alloy. The aluminum alloy you pick will significantly affect both the spreading procedure and the residential properties of the end product. As a result of this, you must make your decision very carefully and take an informed strategy.Establishing the most suitable aluminum alloy for your application will imply weighing a broad array of features. The very first classification addresses alloy features that influence the manufacturing process.
All About Alcast Company
The alloy you select for die casting straight impacts several facets of the spreading process, like just how simple the alloy is to collaborate with and if it is vulnerable to casting defects. Warm breaking, additionally recognized as solidification cracking, is a normal die spreading problem for aluminum alloys that can cause internal or surface-level rips or fractures.Certain light weight aluminum alloys are much more at risk to warm breaking than others, and your selection needs to consider this. An additional common defect discovered in the die casting of aluminum is die soldering, which is when the cast stays with the die walls and makes ejection tough. It can harm both the cast and the die, so you need to search for alloys with high anti-soldering properties.
Corrosion resistance, which is currently a noteworthy feature of aluminum, can vary substantially from alloy to alloy and is an important particular to think about depending on the ecological conditions your product will be exposed to (aluminum metal casting). Wear resistance is another building generally looked for in aluminum items and can set apart some alloys
Report this wiki page